Quality Control
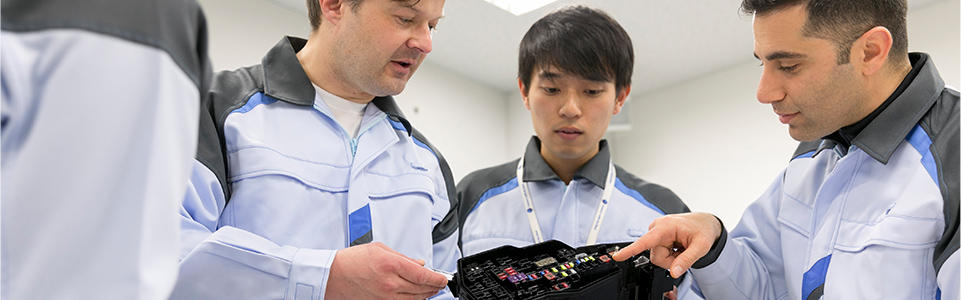
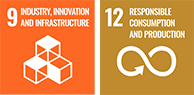
Quality Control
Quality Policies
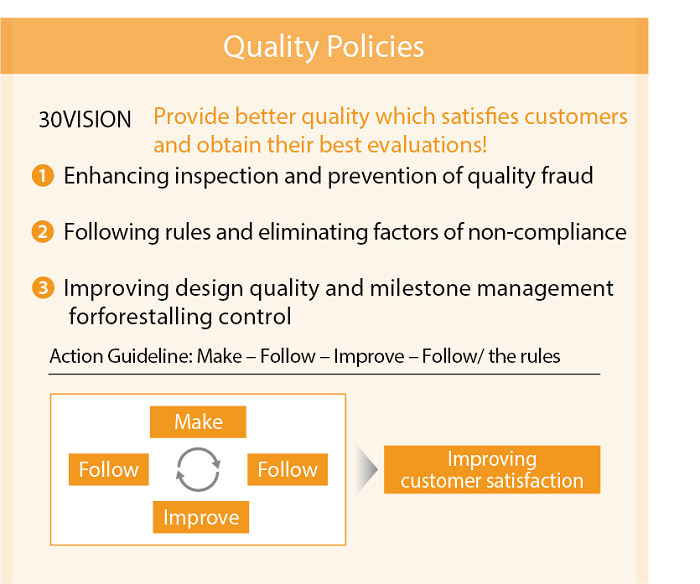
Pursuit of Customer Satisfaction
The number of quality complaints received from customers is gradually decreasing as the Group works to reduce quality defects to improve customer satisfaction.
This is the result of our ongoing efforts to prevent recurrence of quality defects that occurred in the past and to strengthen our product inspection system. On the other hand, there remains the issue of an increase in quality defects when changes occur, such as the launch of new products.
In recent years, in addition to our existing efforts, we have been strengthening activities to prevent quality defects before they occur by improving the accuracy of quality risk verification at the product design stage and at the manufacturing preparation stage of new products. We will continue our efforts to further improve quality to ensure customer satisfaction.
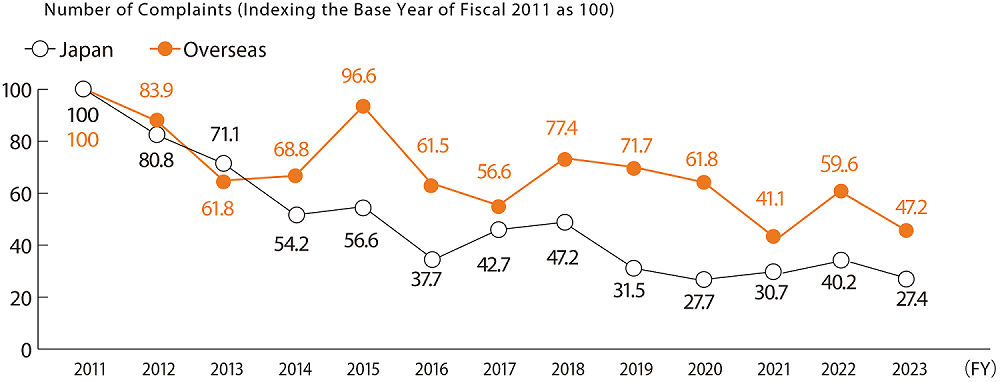
Deepening the Own Process Assurance Activity
The SWS Group promotes the Own Process Assurance Activity as the foundation of achieving zero quality defects.
The design division creates drawings without any elements that might lead to a quality defect (ACT1), the production engineering division makes equipment and processes, which do not allow defects to proceed to the next process, and the manufacturing division develops and operates systems that prevent defects regardless of any change point (ACT2).
To prevent defects, we thoroughly implement 3 Point Control: (1) change point control, (2) abnormality control, (3) work compliance control at manufacturing sites, and visualize them.
As to work procedure and work compliance, we monitor each employee and seek to identify the cause of any non-compliance and improve our standards, jigs and tools, and design.
We will continue to strive for zero quality defects by thoroughly pursuing ACT1, ACT2, and 3 Point Control.
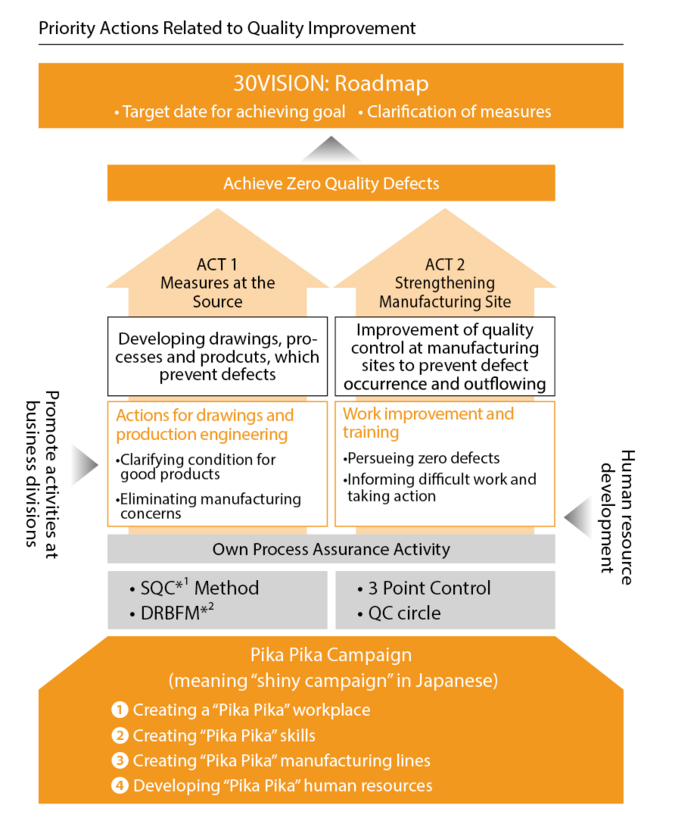
Glossary
*1 Statistical Quality Control
*2 Design Review Based on Failure Modes is used to prevent problems before they happen by learning from failures.
Human Resource Development
Most of our wire harnesses, which are our core products, are manufactured overseas. To realize “globally uniform highest quality“ as a company quality department under these circumstances, we conduct practical on-site training for quality improvement at overseas manufacturing sites.
Specifically, we provide quality improvement training to the leaders of the local manufacturing and quality assurance divisions to eliminate any recurring in-process defects. At first, we conduct quality improvement training focusing on analyzing factors with actual products at the actual site.
After completing the training program, we aim to achieve quality targets and quality improvement through developing improvement methods at each site by following up voluntary improvement activities in which leaders take on roles of trainers.
Activities for Improving Quality Awareness
Compared to Japan, overseas plants have been more affected by high employee turnover, which creates a challenge to maintaining stable quality. Consequently, the SWS Group actively promotes activities for improving quality awareness to realize globally uniform best quality.
Evaluation from Customers
Our group has always strived to provide products that meet high-quality standards and earn the trust of our customers.
As a result, we have earned a high reputation from customers around the world.
We will continue to pursue the provision of products that live up to the trust of our customers.
Pika Pika Campaign for Achieving Globally Uniform Highest Quality
Aiming for the most attractive product and the highest quality in the world, we are promoting the “PIKA-PIKA Campaign” which employees can understand easily.
“PIKA-PIKA Campaign” is a basic idea for our manufacturing, which PIKA-PIKA in mind, behavior, skills, equipment, and factories produces extremely good products.
This campaign consists of four elements: (1)PK evaluation that PK evaluators of the head office review and evaluate the local plants, (2)G-STARS that standardizes basic skills for all the workers and specialized skills for each work process, (3)Human development, (4)Quality improvement (HAI-Q) that is aimed at eliminating defects, which is supported by (3)Human development. In this campaign, all the manufacturing plants conduct improvement activities on a daily basis.
By “(1) PK evaluation”, the on-site conditions such as 5S, facility jigs and tools, daily management, and standard operations are evaluated. By performing the system improvement, such as improvement and rules, we are improving safety and quality, and creating “PIKA-PIKA” (efficient) persons and plant by all the staff.
“(2) G-STARS” is an activity to acquire the basic skills required to work at the manufacturing site.
With the aim of enhancing the motivation for the technological improvement, we are encouraging our employees to acquire certification as a participation in competitions, for which high-technicians gather from all over the world.
Regarding “(3) Human development”, although it is important to have a leader who manages and instructs workers at the manufacturing site, trainers who educate the leader are the most important. We are engaged in activities to educate the trainers.
Regarding “(4) Quality improvement (HAI-Q) that is aimed at eliminating defects”, it is an activity to achieve no defects in process in assembly lines and maintain no defects in process continuously for a long period of time.
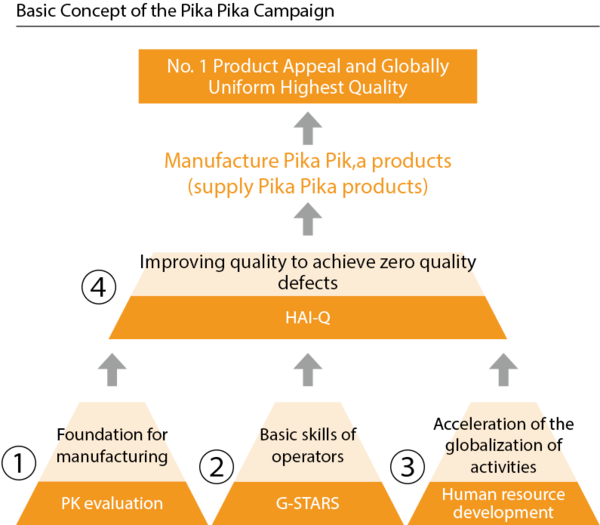
Glossary
*1 G-STARS:Global Skill Training and Recognition System
*2 HAI-Q:Harness Innovation Quality
Research and Development
Basic Stance
As the automobile industry is in a period of great change, we conduct research and development from a global perspective by focusing on proposal-based development that looks ahead to what is needed across the globe in order to meet the diverse needs of societies worldwide and create the corresponding product or service. To adapt to the dissemination of connected cars linked to information and communication networks, the evolution of autonomous cars, lifestyle changes related to cars and the expansion of electrification, we will continue to develop technologies and products to connect and be connected while also leading the way into the new era of mobility.
Research and Development Structure
We work as a team to provide new technologies and products seamlessly for our customers through the integrated efforts of Sumitomo Wiring Systems, in charge of development, design and manufacturing, AutoNetworksTechnologies, in charge of research and development, and Sumitomo Electric Industries, in charge of business planning and sales. In addition, we are working closely with the research department of Sumitomo Electric Industries to promote comprehensive development from materials to parts, modules, electronic equipment and network architecture.
We will enhance our strengths in development and proposals by ensuring that our developers accurately understand customer issues and needs and promptly address them through open innovation, collaboration with academic institutions as well as joint research with parts manufacturers.
In addition to the human resources training of Sumitomo Wiring Systems, we are focused on developing engineers through the original programs of Sumitomo Electric Industries and AutoNetworks Technologies. And we will continue our efforts to develop our workforce.